Day 1 :
Keynote Forum
David G Calatayud
Instituto de Ceramica y Vidrio – CSI, Spain
Keynote: Band-gap engineering and morphological control of TiO2 nanoparticles by a semisolvothermal route
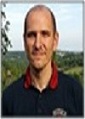
Biography:
Dr. David G. Calatayud received his doctorate in Chemistry from the University of Autonoma de Madrid in 2004 where he studied new asymmetric double-Schiff-bases containing a thiosemicarbazone moiety and their complexes. After completing his PhD he worked as a postdoctoral researcher in the Spanish National Research Council – CSIC, focusing on novel materials, nanotechnology, photocatalytic nanoparticles and crystal engineering. In 2014 he joined Sofia Pascu’s group at the University of Bath (UK) as a Research Associate developing on ‘smart’ all-in-one multimodal imaging probes as novel synthetic platform systems for personalised diagnosis and treatment of diseases such as cancer. In 2016 he moved to the Funceramics group at Instituto de Ceramica y Vidrio – CSIC, his current research is focused on the development of new experimental techniques to assemble functional materials for advanced micro and nanoelectronics, biosensing, molecular imaging and drug delivery applications
Abstract:
TiO2 has become a material of great interest for photocatalytic H2 production, environmental purification and solar energy conversion.[1] It is generally accepted that anatase is the most active photocatalyst of the three possible polymorphs of TiO2. The properties influencing the photoactivity of anatase particles have been reported to include surface area, crystallinity, crystallite size, crystal structure;[2,3] and the morphology of the particles. Among the key parameters boosting the photocatalytic efficiency of anatase nanoparticles, an increased light absorption to extend the optical response to the visible, together with an improved charge separation of the electrons and holes generated upon photoexcitation, shall be enumerated. Conventional TiO2 anatase nanoparticles have a bandgap of 3.20 eV which only allows the excitation of carriers by light with wavelengths smaller than 387 nm (UV region); if visible light harvesting is to be enabled, this gap should be narrowed. In this work, pure anatase nanoparticles have been obtained using a solvothermal process with reduced band-gap and/or reactive faces. Trifluoroacetic acid is used as morphological control and doping agent, and urea is employed as a reduction agent.[4,5] Through the careful choice and control of the working conditions, it is possible to control the final properties of the produced nanoparticles, e.i. morphology, size, crystallinity, crystal phase, network defects and band gap. The obtained results point out that in order to improve the photocatalytic performance, a well-designed intrinsic defective TiO2 system for visible light driven photocatalysis should meet all three requirements simultaneously: (i) reduced band gap for visible light absorption, (ii) appropriate energy level to initiate photocatalytic reaction, and (iii) proper defect species or highly active surfaces to separate photo-generated charge-carriers (electrons and holes) for reaching high catalytic performance.
Keynote Forum
Julian Reinosa
Institute of Ceramics and Glass (CSIC), Spain
Keynote: Effectiveness in UV absorption of hierarchical nano ZnO-microTiO2 composites with photodegradation inhibition
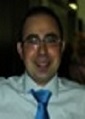
Biography:
Julian J. Reinosa has her expertise in dispersion of nanoparticles, in developing of nanoparticulated microparticles and in obtaining nano and micro hierarchical composites. His studies are centered in the valuation of the developed particles and composites in comparison with microparticles or nanoparticles of similar composition in several fields. Hence, he achieved new effects in ceramics materials thanks to the dispersion and protection of oxides and metallic particles into ceramic glazes; he demonstrated the increase of the yield of UV filters when are correctly dispersed at the same time that the photodegradation is lowered; and he is studying the heating process by applying microwaves energy in particles with different dispersion grade. His expertise joined to other scientist in materials field gave rise to a spin off (AD-Particles) about the dispersion of nanoparticles and the achieving of hierarchical composites for industrial applications
Abstract:
Nowadays, sunscreens are formulated by using TiO2 and ZnO nanoparticles because they are efficient inorganic UV filters. In fact microsized TiO2 and ZnO have been increasingly replaced by TiO2 and ZnO nanoparticles in order to solve the cosmetic drawback of the white opaque sunscreens apart from the higher yield that nanoparticles suppose. Also the aggregation state of the particles in sunscreens is related to the solar protection factor (SPF) of the final emulsion. In this sense, dispersed nanoparticles into sunscreens increase the SPF value, but it means a possible leading to their incorporation into the stratum cornea, the outer layer of the skin. Moreover, when TiO2 is irradiated produces free radicals which are implicated in a number of potential health issues such as skin aging because of the formation of reactive oxygen species (ROS).
In this work, composites combining TiO2 microparticles and ZnO nanoparticles have been achieved by using several synthesis and dispersion methods. It has been demonstrated by the incorporation of the different composites into sunscreens that the presence of nanoparticles anchored over TiO2 microparticles allows increasing the efficiency of nanoparticles but decreases the possible health problems by their absorption as nanoparticles. The aim of these new composites is to gain the advantages of inorganic nanoparticles avoiding their potential drawbacks. Hence, the combination of both oxides provokes higher SPF value and lower photodegradation, in comparison with TiO2 microparticles. Moreover, the disposition of ZnO and TiO2 particles means a positive synergy by the recombination of photo induced electrons holes, which decreases the formation of free radicals.
- Composite Materials| Advanced Ceramic Materials
Location: Rome
Session Introduction
RosalÃa Poyato
CSIC-Universidad de Sevilla, Spain
Title: Effect of the homogenization treatment on the microstructure and the electrical conductivity of 3YTZP/graphene nanoplatelet composites
Time : 11:25-11:55
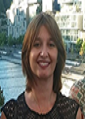
Biography:
Dr. Rosalía Poyato completed her B.Sc. in Physics at the University of Seville and received her PhD in Applied Physics at the Autonoma University of Madrid. After obtaining PhD, she developed her research at University of Connecticut and Ohio State University (USA), as a postdoctoral research Fulbright fellow. At this moment, she is a Tenured Researcher at the Materials Science Institute of Seville and her current research interests include processing and characterization of ceramic composites including carbon nanostructures (carbon nanotubes and multi-layered graphene structures). She has co-authored over 50 papers in international journals. Dr. Poyato is now co-leader of a research project funded by the Spanish National Science Foundation and the European Feder Funding: Processing and microstructural, mechanical and electrical characterization of ceramic-graphene composites (MAT2015-67889-P).
Abstract:
Nowadays, graphene nanoplatelets (GNPs) are being considered as an emerging class of nanomaterials. GNPs are composed of ten or more graphene layers, with thickness up to 100 nm, and present unusual mechanical and electrical properties1,2. These characteristics have motivated a great interest in incorporating these nanostructures as second phase in a ceramic matrix, in order to enhance the mechanical and functional properties of the final composite3-5. However, one of the main obstacles to be overcome is obtaining a good dispersion of the GNPs into the ceramic matrix.
In this work, 3YTZP based composites with different GNP contents were prepared using different powder homogenization methods and electric pulsed discharge sintering (also called spark Plasma Sintering or SPS). Composite powders were prepared by tip-sonication in isopropanol and/or by planetary ball milling under dry or wet conditions. The effect of milling and ultrasonic agitation on GNP integrity and particle size has been evaluated by Raman spectroscopy and laser granulometry. Microstructure of the composites has been analysed by electron microscopy, X-ray diffraction and Raman spectroscopy to assess the integrity of the GNPs, their degree of dispersion or agglomeration in the ceramic matrix and the stabilization of the tetragonal phase in the 3YTZP matrix. The relationships between GNP content and dimensions, microstructure and electrical conductivity, as well as the conduction mechanisms of the composites, have been analysed and discussed.
Atiemo E
CSIR-Building and Road Research Institute, Ghana
Title: Performance of granite dust as filler in ordinary portland cement
Time : 11:55- 12:25
Biography:
Abstract:
Granite dust, a waste from stone crushing accounts for 25% of the final product from stone quarrying in Ghana. In the absence of alternative uses, granite dust which is released directly into the environment has a high tendency of causing environmental pollution. To reduce the impact of the quarry dust on environment and humans, granite dust could be put to alternative uses such as admixture in the production of Portland cement. In this work the physical, chemical, mineralogical, mechanical and durability properties of Portland cement containing varying quantities of granite dust are evaluated. The experimental results indicate that the chemical compositions of all the cement samples are within acceptable limits according to EN 197-1. The raw granite dust also passed the standard chemical composition requirements for pozzolans prescribed by ASTM C 618.Water demand, setting times and soundness of the blended cements containing 5-25% of granite dust were all within acceptable limits per EN 197-1. Compressive strength results indicate that granite dust could be used to replace ordinary Portland cement up to an optimum of 15% for class 32.5 cement. Durability studies after 90 days proved that even though strength decreased as granite dust content increased, the cement samples containing granite dust are stable and can withstand aggressive environments (in terms of percentage strength reduction) comparable to Class 42.5N cement.
Santiranjan Shannigrahi
Institute of Materials Research and Engineering, Singapore
Title: Development of lead-free perovskite ceramics with tunable optical and magnetic properties at room temperature
Time : 12:25- 12:55
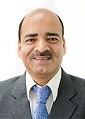
Biography:
Abstract:
In recent days, there have been extensive interests in developing transparent lead free ceramics as the alternatives to toxic lead-based ceramics. Transparent ceramics are fundamental to applications in lasers, sensors, IR optics, and transducers. In this work, La doped sodium potassium niobate based perovskite (ABO3) ceramics, more specifically [{(1-x)(K0.5Na0.5)xLa}Nb(1-2x/5)O3] (0 < x < 0.1) have been developed. Among these, the material at 5 mol% La doping appears with an unusually high density up to 99% of its theoretical value, while densities of the parent K0.5N0.5NbO3 (KNN) ceramics typically only reach ~ 70 to 89% of the theoretical limit. The obtained ceramics display distinctive properties. The developed ceramics in their circular disk form with thickness 0.8 mm show certain transparency and most importantly, this transparency is electrically tunable up to 52%, which is quite remarkable and makes it suitable for optical device applications such as optical filters, sensors and smart windows. Moreover, under UV illumination, the ceramics display a photo-darkening which is reported for the first time for KNN based ceramics. The photodarkening phenomenon is reversible and is time-temperature-transformation phenomena. Additionally, the material shows extraordinary sensitivity of its magnetic and optical properties to UV irradiation. These materials transform to a metastable and reversible state that exhibits graded color change from clear to deep blue and shows considerable increase of magnetization under UV exposure. This feature makes the developed ceramics attractive for the fabrication of new generation devices; e.g. powerless UV detectors as well as protectors, since it absorbs UV completely. Based on first-principles calculations, we developed a model that attributes these observations to the occupancy of La fxyz orbitals induced by UV excitations. The model also indicates that UV induced absorption in the visible range and magnetism are related.
Cristina López-PernÃa
Cristina López-PernÃa, Universidad de Sevilla, Spain
Title: Role of sintering method on graphene/3YTZP composites
Time : 13:40-14:05
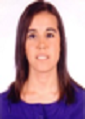
Biography:
Cristina López Pernía is a doctoral candidate at the Department of Condensed Matter at Universidad de Sevilla. She graduated with a Bachelor of Materials Engineering from Universidad Politécnica de Madrid and holds a Master’s Degree in Advanced Materials from Universidad Autónoma de Madrid. Currently she focuses her work on graphene-ceramic composites.
Abstract:
Graphene in the form of graphene nanoplatelets (GNP), graphene oxide or few layer graphene has become an ideal filler in fabrication of different polymer, metal or ceramic composites. Recently, the fabrication of ceramic matrix composites with graphene-based materials has attracted a special interest due to the potential improvement of mechanical and functional properties. Amongst ceramic matrices, 3 mol% yttria tetragonal zirconia (3YTZP) presents outstanding mechanical properties and with the addition of GNP can become electrically conductive. The properties of the materials depend not only on the composition, but also on the microstructure. In the case of ceramics, the processing method has a great importance from the point of view of the final properties. Graphene / ceramic composites are typically prepared through wet powder processing followed by a pressure assisted sintering technique, such as Spark Plasma Sintering (SPS) or Hot Pressing (HP). SPS advantages over HP include lower sintering temperatures and shorter sintering times. However, it requires expensive equipment and produces highly anisotropic materials. Conventional pressureless sintering (PLS) is a simpler and cheaper sintering method that produces composites with lower anisotropy. Therefore, the study of graphene / ceramic composites prepared by PLS compared to SPS sintered ones is very interesting. The main objective of this work is to make a direct comparison of the effects of these two sintering techniques (PLS and SPS) on the microstructural features, mechanical and electrical properties of composites of 3YTZP with different contents of GNPs.
Hasan Metin Tülümen
Karlsruhe Institute of Technology, Germany
Title: Process development for the ceramic injection molding of oxide short fiber reinforced CMCs
Time : 14:05- 14:30
Biography:
Metin Tülümen is a PhD Student at University Freiburg, Germany and working as a research associate in institute of applied materials at Karlsruhe Institute of Technology, working with Prof. Dr. Thomas Hanemann. He earned his Master of Science on materials science and with specialization of glass and ceramics at Clausthal University of Technology, Germany. In his PhD thesis he is developing and characterize new molding compounds containing short ceramic fibers for powder injection processes.
Abstract:
Ceramic matrix composites (CMCs) are created by adding fibers with variety of fiber structure into various ceramic materials to provide condition / task adapted properties. On the other hand, ceramic injection molding is an automated net shaping process that can produce the ceramic parts with complex geometry and good surface quality without the requirement for a post-processing step. In this study, we produced aluminum oxide CMCs (Al2O3 powder: TMDAR, Taimicron; Al2O3 chopped fibers: 3M Nextel 610) by using ceramic (μ-) injection molding process. Each step such as feedstock preparation, molding step, debinding or sintering, has significant effect on the final properties of the CMCs parts. Measurement of density as a function of time, temperature, fiber content or -orientation coupled with the examination of the final microstructure is a useful method to evaluate the ceramic parts. The relative density of sintered CMC parts (sintered from 1150 to 1350 2h) decreased at about 35% with increasing amount of oxide chopped fibers from 0 to 25 Vol. % in feedstock including polymer binding system. The reason of such a low sintering temperature for aluminum oxide based material is to prevent the grain growth in the fibers [1]. In addition, the form of the injection mold design defines the fiber orientation that differentiate the density and mechanical properties of the sintered parts. The difference between tensile specimen (higher orientation) and disc form (random orientation) is about from 1 to 10% depending on temperature and the amount of fiber in the feedstock. On the other hand, whether it is hard to define the mechanical characteristic because of highly deformed sintered parts, our first impression on the results is that the fiber reinforced injection molded parts have lower fracture toughness than common CMC parts with endless fibers or fabric.
Tonle Kenfack Ignas
University of Dschang, Cameroon
Title: Composite materials from clays and clay mineral: Synthesis, characterization and electroanalytical applications
Time : 14:30-15:00
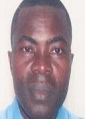
Biography:
Ignas Kenfack Tonle is Professor of Analytical Chemistry at the Department of Chemistry of the University of Dschang (Cameroon) where he leads a research group working on the development of sensors and biosensors based on inorganic porous materials and lignocellulosic materials. In collaboration with the Electrochemistry and Analytical Chemistry research group of Dr Alain Walcarius (University of Lorraine, Nancy- France), his PhD thesis was defended in 2004 at the University of Yaounde 1 (Cameron) under the supervision of Prof Emmanuel Ngameni. The research was focussed on the grafting of organosilanes onto the surface of smectite-type clay minerals, followed by the application of the obtained organoclays as electrode materials in electroanalysis. In 2008, he moved to Prof Christian Detellier’s group (University of Ottawa, Canada) for a one year postdoctoral position. Since 2013, he is a Georg Foster Senior Scientist Fellow to the ‘Elektroanalytik & Sensorik’ group headed by Prof Dr Wolfgang Schuhmann at the Ruhr-Universität Bochum (Bochum, Germany).
Abstract:
Scientific research devoted to the exploitation of clays and clay minerals for the preparation of nanohybrid materials has gained growing for the past decade. The resort to clays minerals as inorganic parent support for such materials is due to their surface reactivity and ability to immobilize guest organic molecules, either within their structure or on their surface. In fact, clay-based nanohybrid materials offer a wide range of applications in environmental protection, catalysis, polymer science and in analytical electrochemistry. In the last mentioned application, the development of amperometric sensors useful in the analysis and determination of various pollutants (e.g. heavy metals, dyes, pesticides) in natural media represents a daily challenge. Yet, the inherent toxic character of these compounds, combined to the relative low degradation rate of some of them and the non-biodegradable character of others made them persistent in living organisms where they participate in metabolism processes, thereby inducing the monitoring and traceability of toxic pollutants is an ethic duty that concerns the whole scientific community and challenges researchers working in several areas covering analytical chemistry, environmental science, pollution control and chemistry of materials. In this communication, some typicalclay-based nanohybrid materials exploited as electrode modifiers for preconcentration electroanalysis will be exposed.
Hasan Metin Tülümen
Karlsruhe Institute of Technology, Germany
Title: Process development for the ceramic injection molding of oxide short fiber reinforced CMCs
Time : 14:05- 14:30
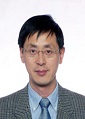
Biography:
Metin Tülümen is a PhD Student at University Freiburg, Germany and working as a research associate in institute of applied materials at Karlsruhe Institute of Technology, working with Prof. Dr. Thomas Hanemann. He earned his Master of Science on materials science and with specialization of glass and ceramics at Clausthal University of Technology, Germany. In his PhD thesis he is developing and characterize new molding compounds containing short ceramic fibers for powder injection processes.
Abstract:
Ceramic matrix composites (CMCs) are created by adding fibers with variety of fiber structure into various ceramic materials to provide condition / task adapted properties. On the other hand, ceramic injection molding is an automated net shaping process that can produce the ceramic parts with complex geometry and good surface quality without the requirement for a post-processing step. In this study, we produced aluminum oxide CMCs (Al2O3 powder: TMDAR, Taimicron; Al2O3 chopped fibers: 3M Nextel 610) by using ceramic (μ-) injection molding process. Each step such as feedstock preparation, molding step, debinding or sintering, has significant effect on the final properties of the CMCs parts. Measurement of density as a function of time, temperature, fiber content or -orientation coupled with the examination of the final microstructure is a useful method to evaluate the ceramic parts. The relative density of sintered CMC parts (sintered from 1150 to 1350 2h) decreased at about 35% with increasing amount of oxide chopped fibers from 0 to 25 Vol. % in feedstock including polymer binding system. The reason of such a low sintering temperature for aluminum oxide based material is to prevent the grain growth in the fibers [1]. In addition, the form of the injection mold design defines the fiber orientation that differentiate the density and mechanical properties of the sintered parts. The difference between tensile specimen (higher orientation) and disc form (random orientation) is about from 1 to 10% depending on temperature and the amount of fiber in the feedstock. On the other hand, whether it is hard to define the mechanical characteristic because of highly deformed sintered parts, our first impression on the results is that the fiber reinforced injection molded parts have lower fracture toughness than common CMC parts with endless fibers or fabric.
- Ceramics applications| Porous Ceramics | Ceramic Industry and Environment
Location: Rome
Session Introduction
Danjela Kuscer
Jozef Stefan Institute, Slovenia
Title: Fabrication and characterisation of high-frequency ultrasonic transducers based on piezoelectric thick films and porous backing
Time : 15:00-15:30
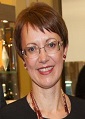
Biography:
Asst. Prof. Danjela Kuscer, PhD in material science at the University of Ljubljana, Slovenia (1999). Current position: senior researcher at Jožef Stefan Institute and Assistant Professor at Jožef Stefan International Postgraduated School, Ljubljana, Slovenia.
Research: synthesis and characterisation of complex-composition ceramic applicable in electronics, including synthesis of (nano) powders by mechanically-assisted and solid state synthesis, synthesis of ceramic with tailored microstructure, patterning of thick film structures using water- and organic-based suspensions by electrophoretic deposition, screen- and inkjet printing, and their structural, microstructural and functional characterisation.
Publications: 120 publications and 150 technical reports. She holds one Slovenian, two USA patents and three PCT patent applications.
She participated in 31 projects, of which she leads 7 EU and 5 national applied projects.
Between 2014 and 2017 she won six national awards for the innovation in the field of ceramics, the most important being Puh recognition for 2015, the highest Slovenian science award for important applied work.
Abstract:
The properties of the high-frequency transducer (>20 MHz), in particular its operating frequency, sensitivity and resolution, are defined by the geometry, microstructure and characteristics of piezoelectric material and backing. For the backing, acoustical impedance and attenuation coefficient are predominant properties to be determined. In this work, we proposed a novel method for the in-situ measuring of these backing’s properties at the operating frequency of the transducer.
We report on the processing and characterization of lead-zirconate-titanate based (PZT) piezoelectric thick films on a porous backing with tailored amount, size and shape of the pores. As a porous backing we used ~5mm-thick ceramic with nominal composition Pb(Zr0.53Ti0.47)O3 (PZT). The ceramic was prepared by hetero-coagulation process of PZT and polymethilmetacrylate in water at pH 8 followed by sintering the powder compacts at 1080 oC. Ceramic exhibited homogeneous microstructure with 15 % porosity and spherical, ~1 and ~10 mm-sized pores, respectively. The PZT thick films, screen-printed onto the electroded backing and sintered at 900 oC, had a thickness of ~25 mm, porosity of 20 % and thickness coupling coefficient of 45 %.
This integrated piezoelectric structure allows direct acoustic measurements of transducer components. The PZT thick film is electrically excited to measure the electroacoustic response in water and also the back-wall echoes coming from the backing if its thickness is sufficiently thin. The thickness of the backing was successively reduced and the measurements were repeated.
In the frequency range 15-25 MHz, the attenuation coefficients of backings with 1- and 10-mm- sized pores were 0.7 dB/mm/MHz and 4 dB/mm/MHz, respectively, the group velocities were ~3400 m/s which results in the acoustic impedance of ~22 MRa. The high attenuation in backing with 10 mm-sized pores and moderate acoustical impedance enable substantial miniaturisation of high-resolution ultrasonic imaging transducers.
Xiao Huang
Shanghai Institute of Ceramics, China
Title: Preparation of zZirconium-based porous ultra-high temperature ceramics via sol-gel precursors
Time : 15:30-16:00
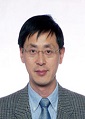
Biography:
Abstract:
Ultra high temperature ceramics (UHTCs) are a class of inorganic materials that have melting point over 3000 °C and are typically borides, carbides and nitrides of early transition metals. UHTCs are considered as the promising candidate used in the extreme environment involved with the hypersonic aviation thermal protective system. Synthesis of UHTC based materials can be divided into solid based and solution based protocols according to the state of the raw materials. Sol-gel process is one of the solution based protocols for the preparation of UHTC based materials, which involves the hydrolysis, condensation of the metal organic and/or metal inorganic compounds, gelation and the post high temperature treatment of the dried gels. Here, we present the preparation of several zirconium-based porous UHTCs. The formation and manipulation of the pore structure and the correlation to their properties are also discussed.
Maria Vartanuan
D. Mendeleev University of Chemical Technology of Russia, Russia
Title: Practical approaches to energy efficiency improvement in SiC-based ceramics processing
Time : 16:15-16:45
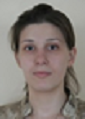
Biography:
Maria Vartanyan is an expert in ceramics manufacturing, energy efficiency and environmental performance in production of ceramics materials based on oxide and non-oxide compounds.
Abstract:
Statement of the Problem: Glass and ceramic industries fall into the category of energy-intensive industries and since 2014 when Integrated Pollution Prevention and Control was introduced in Russia these sectors have been closely monitored with regards to resource efficiency and environmental performance. Methodology & Theoretical Orientation: Traditional sub-sectors including tile and brick manufacturing in 2003-2013 participated in pilot projects intended to evaluate possibilities of implementing Best Available Techniques (BATs) in Russian industries. Based on the results of these projects BATs have been identified and national Information and Technical Reference Books developed. In manufacturing technical ceramics existing sector-specific BATs comprise mostly emissions control. However, considering materials for advanced applications such as alumina, zirconia or carborundum, where these levels are determined by strict process parameters, a generally accepted practice is to reduce energy consumption by adjusting firing temperature. This allows to suggest candidate BATs: batch composition adjustment, the use of eutectic sintering aids, and liquid-phase sintering. Findings: The present research addresses a combination of these techniques in production of SiC-based structural ceramics including selection of additives based on their physico-chemical properties (melting point, surface interaction) and the use of pre-fabricated sintering aids with enhanced reactivity. The effects of the additives on sintering behavior, phase composition, microstructure, and mechanical properties were studied. Conclusion & Significance: The combination of ultrafine SiC with 25 vol. % of a eutectic sintering aid in MgO-Al2O3-Y2O3 system allowed to produce ceramics with bending strength of 450 MPa, fracture toughness of 4.0 MPa·m1/2, and elasticity modulus of 380 GPa. Sintering temperature for this material didn’t exceed 1900 °C, which makes this technique practically suitable to reduce emissions and the impact on the environment. This research was carried out with financial support from the Ministry of Education and Science of the Russian Federation under State order, contract No. 10.6309.2017/BCh.
Dieraert Axel
CEA, DAM
France
Title: printing of ceramic-based porous structures using stereolithography
Time : 16:45-17:10
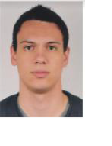
Biography:
Axel Dieraert obtains his Master’s degree in inorganic chemistry in 2016 at the University of Montpellier, in France (major of promotion, specialty “Porous materials, divided systems and thin layers”). Since 2017, he’s PhD student at CEA Le Ripault (“Commissariat à l’Energie Atomique et aux Energies Alternatives”), under the direction of Philippe Belleville (CEA Le Ripault – PhD director) and Clement Sanchez (UPMC Paris - scientific adviser). The purpose of this thesis is to develop new materials for high temperature insulation based on stereolithography of ceramic materials.
Abstract:
Stereolithography-based additive manufacturing (AM) is increasingly becoming the technology of choice for the small series or single unit production. It also allows the material-by-design fabrication, prime concern for most material chemists. State-of-the-art of three-dimensional (3D) structured organic-inorganic hybrid materials will be described and focus onto combined 3D printing technology and sol-gel ceramic-based material preparation will be emphasized.
Although the spectrum of available 3D-printed materials has been widened in recent years, there is still a lack of ceramic-based materials which can be processed with stereolithography on a routine basis. The extremely high melting point of many ceramics adds challenges to additive manufacturing as compared with metals and polymers. Because ceramics cannot be cast or machined easily, three-dimensional (3D) printing enables a big leap in geometrical flexibility and microstructured architecture.
We report work on synthesis new ceramics from preceramic monomers or inorganic nanopowder loaded resins that are cured with ultraviolet light in a stereolithography 3D printer. After a thermal debinding and sintering step the part turns into a dense ceramic open structure and gains its final properties, with uniform shrinkage and porosity control.
The paper discusses the critical process parameters that influence polymerization uniformity and structure quality. Currently it is possible to print 3D-structures with a spatial resolution down to 40 μm, with complex shape and cellular architecture. The photosensible resin formulation is a key parameter to control the printing resolution, so the geometry of the final ceramic. Highly complex three-dimensional open microstructures have been theoretically designed to lead to the best agreement between thermal insulation properties and mechanical toughness.
Experimental characterization and performances of the AM ceramic parts will be discussed with regard to high temperature super insulation material application, exhibiting high-stiff properties.
Finally, scale-up of this combined approach is carefully considered.